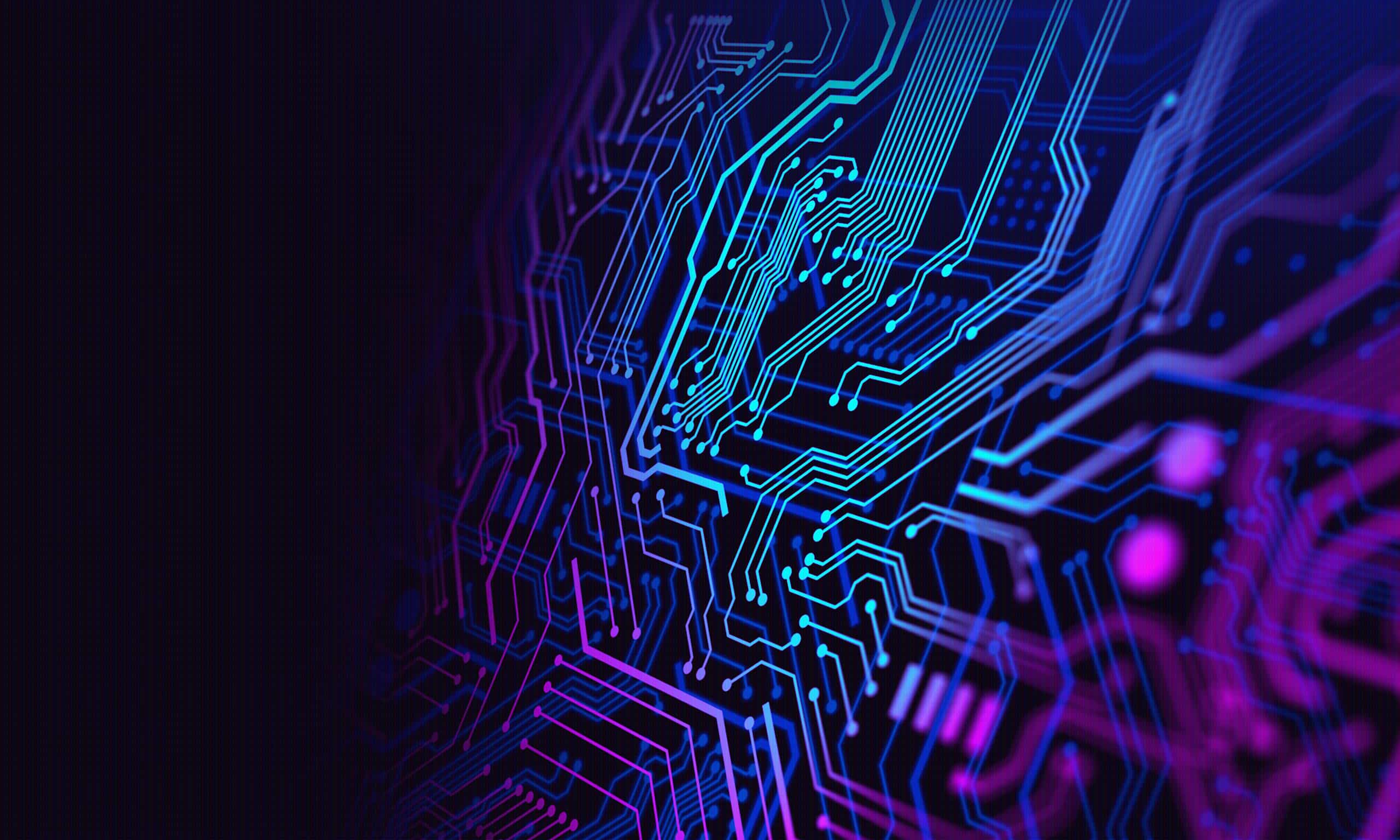
Flexible electronics is a rapidly evolving technology that enables circuits and components to be built on bendable, stretchable, or conformable surfaces. Unlike traditional electronics, which are fabricated on rigid substrates like glass or silicon wafers, flexible electronics use pliable materials such as plastic films, metal foils, or even textiles and paper.
This shift in substrate—from rigid to flexible—opens up new design possibilities and radically expands where and how electronics can be used. Whether it’s a skin-adhering medical patch, a rollable display, or a smart label that wraps around a bottle, flexible electronics bring function to form in entirely new ways.
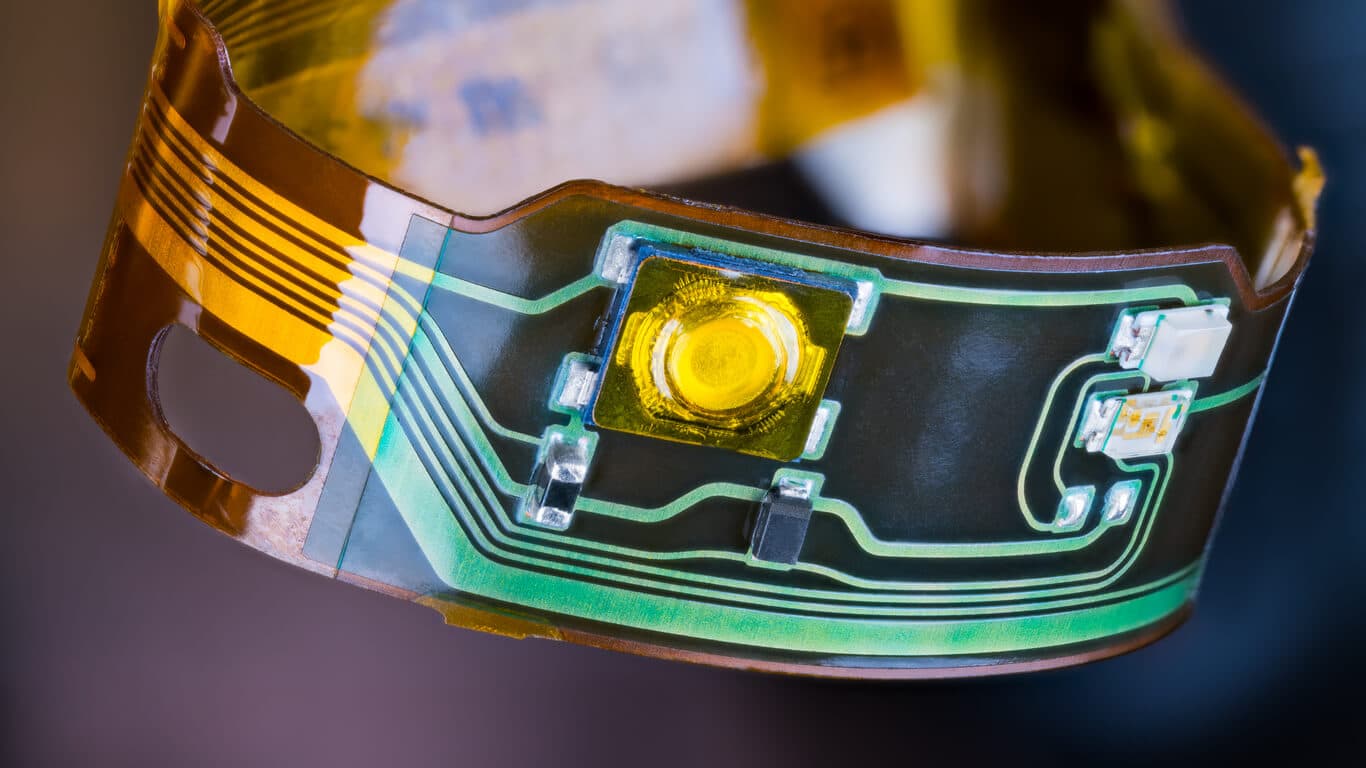
A New Paradigm: Flexible vs. Rigid Substrates
Conventional electronics rely on flat, inflexible substrates. These are excellent for performance and precision but limit where and how devices can be applied. For example, rigid substrates are impractical for wearable health monitors, smart clothing, or packaging that needs to bend and fold.
Flexible electronics remove this constraint. By using substrates like PET, PEN, polyimide, or paper, these systems allow electronics to wrap, roll, and stretch—while remaining operational. This flexibility also makes them more durable in dynamic environments where movement, impact, or shape change is expected.
Designers are no longer confined to flat surfaces or rectangular circuit boards. Instead, they can create devices that follow the human body, conform to curved industrial components, or integrate directly into soft materials.
Key Application Areas
Flexible electronics unlock value in sectors where form factor, weight, and adaptability matter. Common applications include:
Wearables
- Skin-like fitness and medical sensors
- Smart textiles with embedded circuits or heaters
Healthcare
- Soft biosensing patches
- Conformal ECG/EKG monitors
- Bandages with diagnostics or drug-release functions
Consumer Devices
- Foldable or rollable displays
- Thin, flexible battery packs and antennas
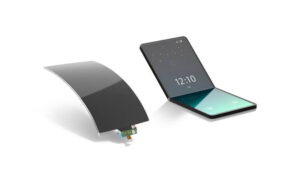
Industrial and Automotive
- Flexible lighting and dashboards
- Sensors integrated into curved surfaces for diagnostics
Smart Packaging
- Labels with printed NFC, RFID, or condition indicators
- Curved smart tags and authentication elements
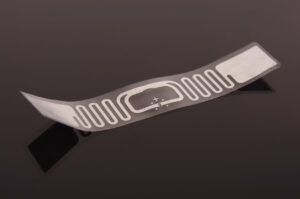
Energy and Environment
- Flexible solar panels for curved surfaces or mobile charging
- Lightweight energy storage integrated into enclosures
How Flexible Electronics Are Made
At the heart of flexible electronics is the ability to deposit active materials onto soft substrates. This is accomplished using a range of methods, including:
Printing-Based Techniques
Screen printing, inkjet printing, and aerosol jet printing are widely used to deposit conductive, semiconductive, and dielectric inks on flexible substrates. These additive methods are efficient, customizable, and scalable.
Thin-Film Deposition
Vacuum-based techniques like sputtering or chemical vapor deposition are still used, especially when higher performance is needed. These processes can be adapted for roll-to-roll or sheet-based flexible substrates.
Hybrid Integration
Flexible systems often incorporate a mix of flexible components and small rigid chips. This allows the system to maintain flexibility while achieving high-speed logic or data processing through conventional silicon chips, bonded or mounted selectively.
Materials in Flexible Electronics
A key enabler of flexibility is the set of functional materials that can be processed at low temperatures and remain stable under mechanical stress:
- Substrates: PET, PEN, PI, TPU, and specialized papers
- Conductive inks: Silver, gold, platinum, copper, carbon, and CNTs
- Semiconductors: Organic molecules, metal oxides, hybrid perovskites
- Insulators/Dielectrics: Flexible polymers or nanocomposite films
- Barrier/Encapsulation layers: To prevent moisture or oxygen intrusion while maintaining stretchability
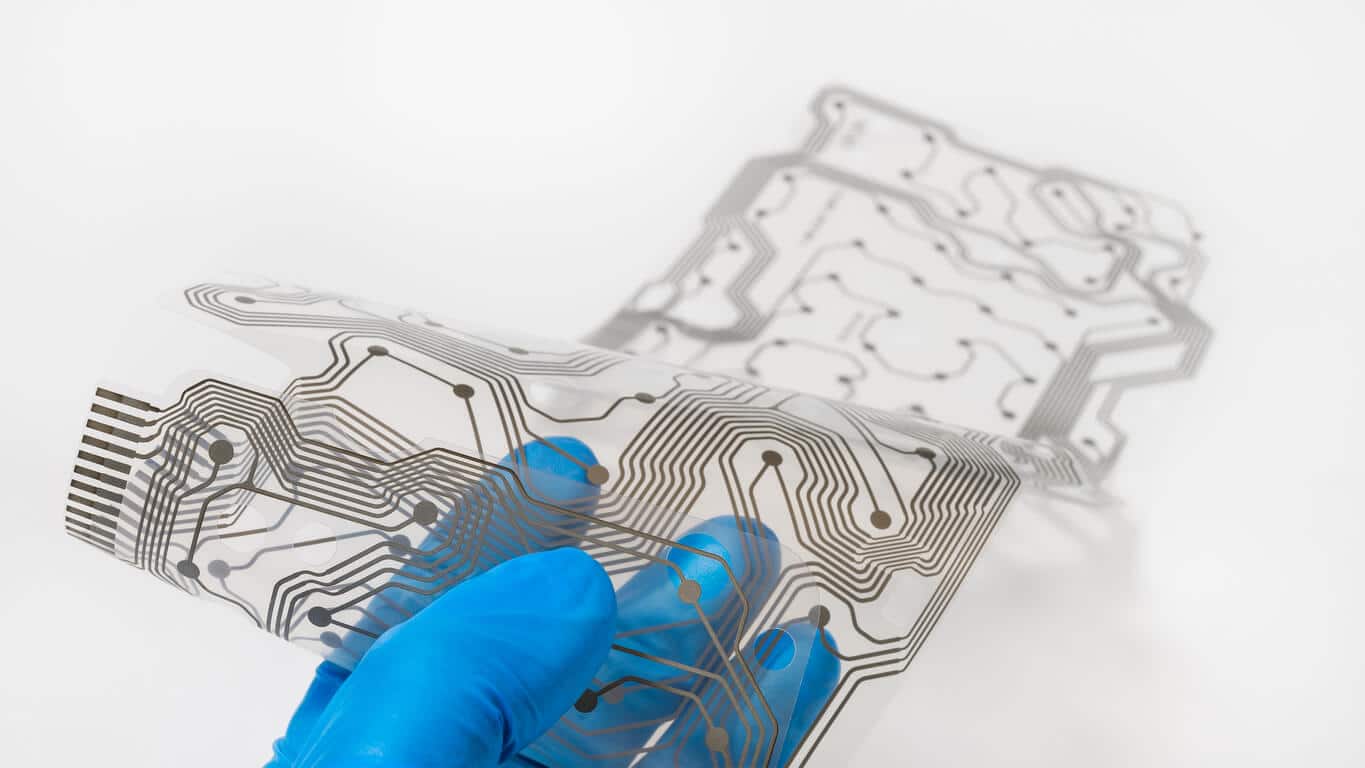
Why Flexible Electronics?
The shift from rigid to flexible electronics brings multiple benefits:
- Form Factor Freedom: Devices can follow curved surfaces or be worn on the body
- Thin and Lightweight: Enables unobtrusive design and integration into small spaces
- Mechanical Robustness: Absorbs shocks and strain better than brittle rigid substrates
- Production Efficiency: Many processes are compatible with roll-to-roll or sheet-fed manufacturing
- Customization: Printing methods allow for rapid prototyping and on-demand design changes
Evolution and Industry Momentum
The field has grown significantly in the past two decades, driven by advances in materials, printing, and design software:
- 2000s: Academic exploration of organic semiconductors and flexible circuits
- 2010s: Commercial entry of smart labels, wearable patches, and foldable displays
- 2020s: Mainstream adoption of flexible phones, and deeper integration in healthcare, logistics, and wearables
Importantly, flexible electronics are no longer viewed as low-performance novelties. Many modern designs rival their rigid counterparts, especially when hybrid approaches are used.
Challenges and What Lies Ahead
Even with its advantages, flexible electronics face hurdles:
- Reliability: Devices must endure repeated bending, stretching, and environmental exposure
- Material Compatibility: Different layers must expand and contract together
- Interface Complexity: Interconnecting flexible and rigid components can be delicate
- Standardization and Testing: Industry norms are still catching up with innovation
As materials improve and the ecosystem matures, flexible electronics will help define the next generation of interactive, comfortable, and embedded technology—shaping a future where electronics no longer sit on the product, but become part of it.
Conclusion
Flexible electronics mark a fundamental shift in how and where electronics can be deployed. They expand the design space beyond the flat and rigid, enabling integration into soft, mobile, curved, and even stretchable surfaces.
This new paradigm will play a critical role in healthcare, consumer devices, packaging, and sustainable energy—blending seamlessly into the world we live in, rather than asking us to adapt to the device.
As research and commercialization continue to converge, flexible electronics will become central to the next wave of personalized, portable, and pervasive technology.